Understanding Protective Coatings for Machinery
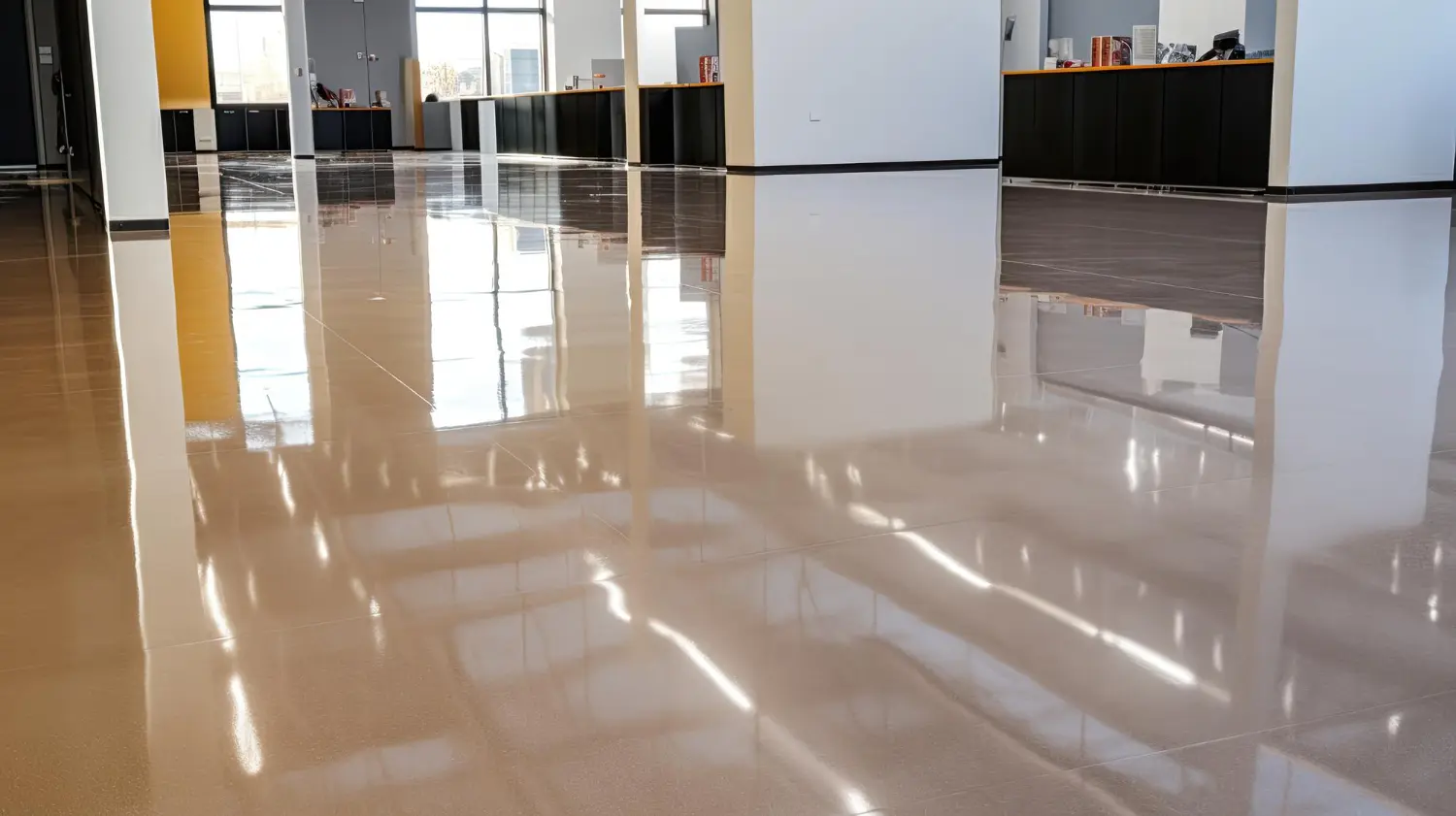
Protective coatings play a vital role in maintaining the longevity and performance of machinery. Whether you operate a factory, a workshop, or any industrial environment, keeping machinery in top condition is crucial. Over time, equipment is exposed to harsh conditions, including moisture, chemicals, and physical wear and tear. Applying the right protective coating can significantly extend the life of your machinery and enhance its efficiency.
One of the key reasons to use protective coatings is to prevent rust and corrosion. Metal machinery is especially prone to corrosion when exposed to moisture and chemicals. Once machinery starts to corrode, it can quickly lose its functionality and strength. Protective coatings create a barrier that shields the equipment from these damaging elements.
Additionally, protective coatings can improve the appearance of machinery. A well-coated machine looks clean and professional, which can boost employee morale and impress visiting clients. Beyond aesthetics, a uniform coating can also be a part of routine maintenance, making it easier to spot potential issues before they become severe problems.
In this article, we will explore different types of protective coatings for machinery, their benefits, application methods, and how to choose the right coating for your specific needs. Understanding these aspects can help you make informed decisions that will protect and preserve your valuable equipment for years to come.
Types of Protective Coatings for Machinery
There are various types of protective coatings available for machinery, each designed to address specific challenges. Knowing these different types can help you choose the best option for your equipment needs.
- Epoxy Coatings: Epoxy coatings are popular for their durability and resistance to chemicals. They form a thick, hard layer that is excellent for protecting surfaces exposed to harsh conditions. Epoxy coatings are often used in industrial settings due to their long-lasting protection.
- Polyurethane Coatings: These coatings offer great flexibility and impact resistance. Polyurethane is especially effective in environments where machinery is subject to physical stress. It provides a glossy finish that can enhance the appearance of your equipment while offering robust protection.
- Ceramic Coatings: Ceramic coatings are known for their ability to withstand high temperatures. They are perfect for machinery that operates under extreme heat. These coatings not only protect against thermal damage but also offer good wear resistance.
- Zinc Coatings: Often used as a primer, zinc coatings provide excellent rust and corrosion prevention. They are commonly applied to machinery that will be painted over with other types of protective coatings. Zinc acts as a sacrificial layer, corroding first and thus protecting the underlying metal.
Benefits of Using Protective Coatings
Protective coatings offer numerous benefits that go beyond mere aesthetics. Here are some of the key advantages of applying protective coatings to your machinery:
- Corrosion Resistance: One of the most significant benefits is corrosion resistance. By shielding machinery from moisture and chemicals, protective coatings prevent rust and corrosion, which can cause significant damage over time.
- Extended Lifespan: Protective coatings can greatly extend the lifespan of your machinery. By minimizing wear and tear, these coatings help your equipment remain functional for longer periods, reducing the need for frequent replacements.
- Improved Efficiency: Well-maintained machinery tends to operate more efficiently. Protective coatings help in reducing friction and surface damage, leading to smoother operations and less energy consumption.
- Cost Savings: The reduced need for repairs and replacements leads to substantial cost savings. Investing in high-quality protective coatings can save you money in the long run by lowering maintenance costs.
- Enhanced Safety: Coated machinery is safer to operate. Protective coatings can prevent slipping and other hazards that might occur if surfaces were corroded or damaged. This contributes to a safer working environment for your employees.
By understanding the types of coatings available and their benefits, you can make informed decisions to protect your machinery effectively.
Application Methods for Protective Coatings
There are several methods for applying protective coatings to machinery, each with its own advantages and practical uses. Understanding these methods can help ensure that coatings are applied effectively, providing the best protection for your equipment.
- Brushing and Rolling: This traditional method is best for smaller or more intricate parts of machinery. Brushing allows for precise application in hard-to-reach areas, while rolling is useful for covering larger surfaces quickly. However, this method may not provide the smooth finish that some other methods can achieve.
- Spraying: Spraying is a popular method for applying protective coatings, especially for larger surfaces. It ensures an even and fine coat, reducing the risk of missed spots. Types of spraying include air spraying, airless spraying, and electrostatic spraying. Each type can be chosen based on the material and desired finish.
- Dipping: This method involves submerging the entire piece of machinery in a vat of coating material. Dipping ensures thorough coverage, making it suitable for parts with complex geometries. It’s often used for smaller parts or when precision coverage is crucial.
- Powder Coating: Powder coating involves applying a dry powder to the metal surface, which is then cured under heat. The result is a hard, durable finish that is resistant to chipping and scratching. This method is widely used for automotive parts and other industrial components.
Choosing the Right Coating for Your Machinery
Selecting the right protective coating depends on several factors. Making the right choice can ensure optimal performance and longevity for your machinery. Here are the key considerations:
- Environment: Consider the conditions in which the machinery will operate. For example, machinery exposed to chemicals or extreme temperatures might require epoxy or ceramic coatings.
- Material: The type of material your machinery is made from will impact your choice of coating. Metal machinery exposed to moisture might benefit from zinc coatings to prevent rust.
- Durability Needs: Assess the level of wear and tear your machinery will endure. If the equipment is subject to heavy physical stress, polyurethane coatings may offer the necessary resilience.
- Application Method: Depending on the complexity and size of the machinery, certain application methods might be more practical. Spraying might be efficient for large surfaces, while brushing could be better for detailed areas.
- Aesthetic Requirements: Some environments or industries require machinery to maintain a certain appearance. In such cases, a coating that provides a smooth, glossy finish might be desirable.
Final Thoughts
Understanding the various types of protective coatings and their respective benefits is essential for maintaining the longevity and efficiency of your machinery. Different application methods and careful consideration of factors specific to your needs can help ensure that your equipment remains in optimal condition.
Investing time in selecting the right coating and application method can save significant costs associated with repairs and downtime. Protecting your machinery effectively not only extends its lifespan but also contributes to a safer and more efficient workplace.
For professional advice and top-notch protective coating services, reach out to Armortough Coatings. Our experts are ready to help you choose and apply the best coatings to safeguard your machinery for years to come!